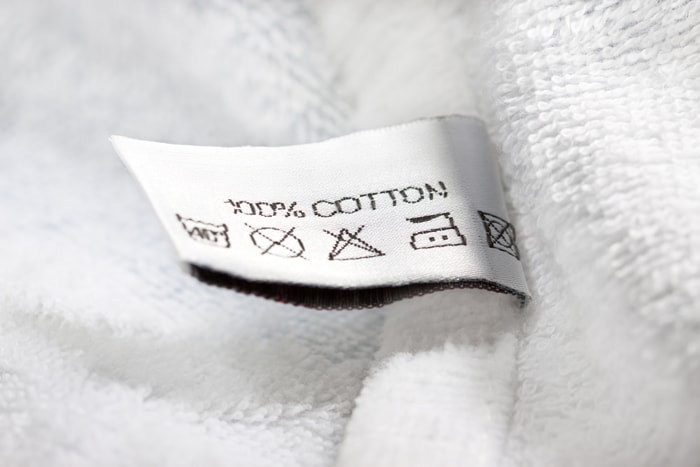
Bringing you the benefits that come from decades of experience and a proven track record
Our experts are among the most knowledgeable in the world when it comes to gas-enabled applications. Here you will find a wealth of information on the process innovations and application expertise they have brought to Cleaning, Polishing & Grinding. Simply click on the Processes and discover how we can help you meet your quality, efficiency and optimisation targets.
Cryocleaning
During the printing process most parts of the printing press get contaminated by all kinds of
substances like dried ink, paper dust, grease, oil, coatings, varnish, etc.
The conventional cleaning methods need aggressive solvents which are toxic, hazardous and can be flammable.
An additional problem are long downtimes. Using dry ice cleaning takes away most of those problems and gives
substantial benefits to the user.
The cleaning agent (dry ice pellets) is very soft like plaster, thus
creating no scratches, wear or damages, even on sensitive surfaces.
When the cylinders are removed all surfaces are accessible and can be cleaned in a fraction of the time
needed before. This gives a dramatic reduction in downtime. Further savings will result from the absence of
disposal costs.
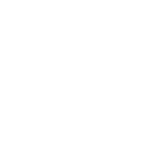
Did you know?
● To produce crumb rubber, it is necessary to reduce the size of the tire shred or
chip. This is accomplished by techniques called cryogenic grinding.
● Cryogenic processing refers to the use of liquid nitrogen (−196°C) to freeze tire chips prior to
size reduction. The rubber is immersed in liquid nitrogen to reduce the temperature of the tire chip. The
cooled rubber is then ground in an impact-type reduction device.
Dry ice cleaning
The dry ice cleaning process CRYOCLEAN® increases the output of a printing machine substantially by simultaneously reducing costs for the cleaning. Cryogenic grinding can achieve a very fine level of grind as most hardy materials tend to become brittle when cooled with liquid nitrogen. Waste materials can be separated by exploiting the coldness of liquid nitrogen. Cryogenic grinding can achieve a very fine level of grind as most hardy materials tend to become brittle when cooled with liquid nitrogen.
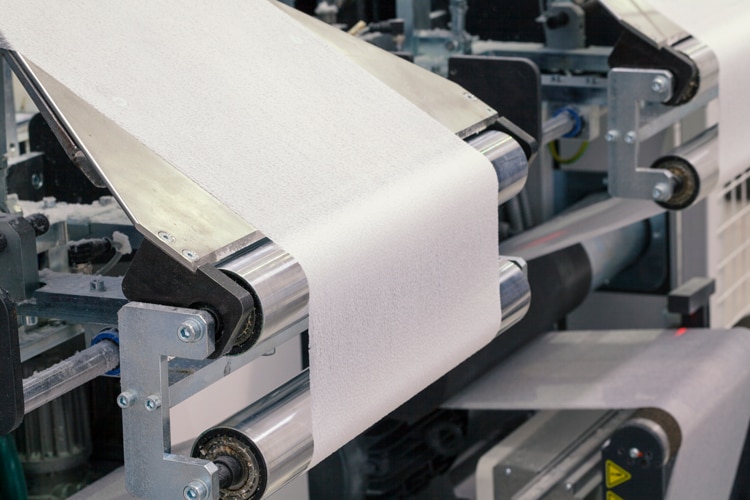
Bleaching
Ozone is an attractive alternative to chlorine-containing chemicals as a way to bleach pulp and achieve the necessary level of brightness. It is widely used for both TCF and ECF bleaching. As it is an extremely effective bleaching agent, ozone reduces the volume of other bleaching chemicals required.
Grinding
Cryogens can be an effective way to reduce the size of materials that cannot be ground under normal conditions. Many materials that are resilient at ambient temperatures become brittle and glass-like under low temperatures. As a result, these materials can be pulverised through impact or shearing. This form of grinding can also be used to create unusual particle shapes or sizes.
Various materials are suited to cryogrinding. For instance, materials that are tacky or oily can often be solidified and ground. Products that are heat-sensitive can be processed at a temperature level that allows them to be ground without degrading or melting. In addition, cryogenic impact can debond multicomponent materials such as chrome-plated ABS (plastic). And spices can be ground without loss of volatile oils and flavours, thus preserving and enhancing their quality.
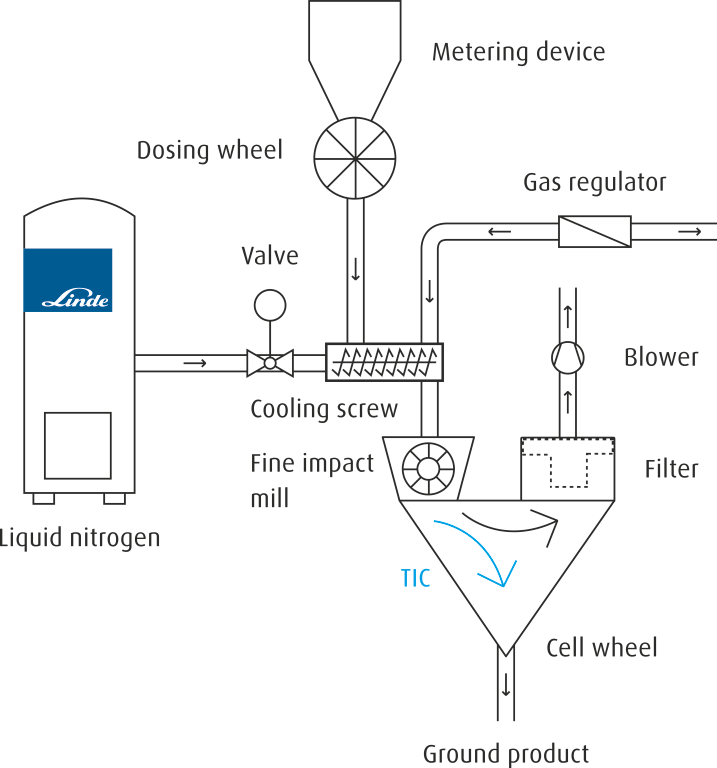
Liquid nitrogen
The most widely accepted refrigerant for cryogrinding is liquid nitrogen (–196°C). Unlike CO2, liquid nitrogen (LIN) does not go through a solid phase, instead transitioning directly to a gaseous state. LIN can thus be directly injected into a grinding mill. During the solid-to-gas phase change, it produces a powerful cooling effect on the product. Solid carbon dioxide (also known as dry ice) or liquid CO2 can also be used as grinding coolants if temperatures below –78°C are not required. We deliver a tailored, dedicated supply concepts for cryogrinding installations, extending from gas supply and storage systems through supply lines to pressure and temperature control solutions.
Buy products here
Downloads
Safety datasheets | Product datasheets & brochures |
---|---|
|